Aluminium producers, smelters, waste incinerators, and others are partnering with Bilfinger to develop innovative solutions and manufacture refractory elements that enhance competitiveness in the green transition. Bilfinger refractory expertise is increasingly in demand.
Crafted at the Herøya workshop
Bilfinger recently delivered a major order of refractory boxes produced at their Herøya workshop in Porsgrunn.
“These are refractory boxes for a filter that purifies molten aluminium,” explains the refractory team—Morten Skifjeld, head of the Porsgrunn division; Morgan Halvorsen, workshop supervisor; and Stian Herum, project manager.
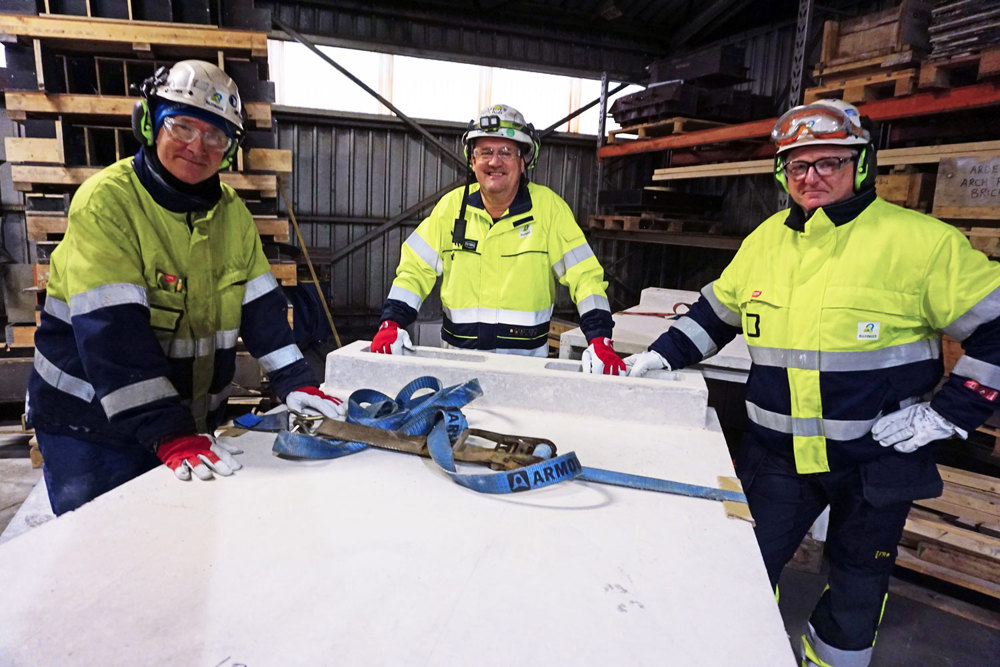
The filter is assembled by a company in Sunndalsøra that supplies filtration solutions globally. This results in cleaner aluminium.
Recycled materials in demand
Bilfinger works closely with forward-thinking customers and suppliers on aluminium recycling.
“Recycled materials are definitely in demand,” says Herum, highlighting exciting collaborations with clients.
“One of our customers is increasing capacity to handle and recycle more scrap, supported by excellent filtration systems. It’s just one of several exciting partnerships we have. More and more clients are demanding recycled and green aluminium products. Take Mills mayonnaise tubes—they proudly advertise as 100% recycled!” says Herum enthusiastically.
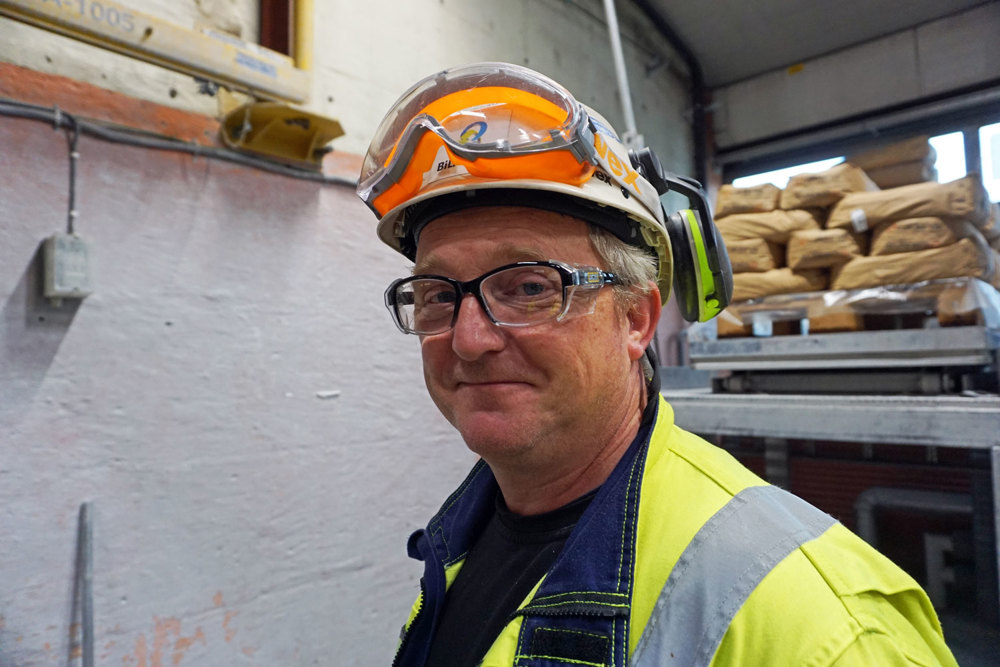
Norway’s largest aluminium supplier
Proud refractory colleagues state they are by far the largest and most capable supplier to the aluminium industry in Norway.
“There’s no competition! We handle all refractory maintenance at every Hydro plant in Norway producing aluminium and have dedicated workshops at each location. We manage everything related to refractory work,” they emphasise.
Growing demand
Bilfinger Refractory boasts an impressive client list, including Yara, Ineos, Inovyn, Equinor, Benteler, and Vianode, as well as customers in waste incineration and crematoria.
“We’re experiencing significant demand and are continuously expanding,” the team says. “The number of clients and the scope of projects are growing. More companies see what we deliver and choose us.”
In 2023, maintenance and project contracts with major players like Hydro, Eramet, and Speira were renewed for five more years.
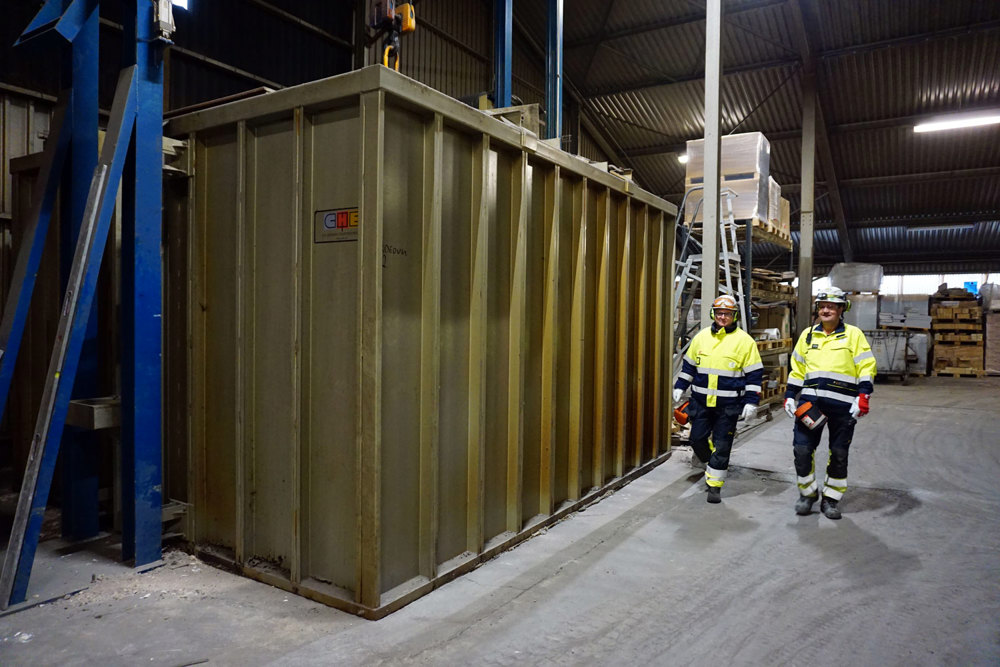
Producing unique refractory parts
Bilfinger’s Herøya workshop features a large prefabrication facility producing unique components for other Bilfinger workshops, such as those in Karmøy, Årdal, Sunndalsøra, and Høyanger. These parts are critical for oven installations.
“What’s unique about refractory materials is that they must undergo drying and firing,” explain Herum and Skifjeld. “All moisture must be removed; otherwise, it can cause explosions in aluminium ovens.”
Significant savings
The refractory team also creates unique parts and repairs oven components in operation.
“We can save customers a week of ramp-up time by ensuring ovens are operational much faster. This is a clear improvement and a huge value that our clients increasingly recognise,” says Herum. “Helping Hydro and others minimise downtime, with quick turnaround times, is a major win. We’re constantly refining this process to save even more time and increase production efficiency.”
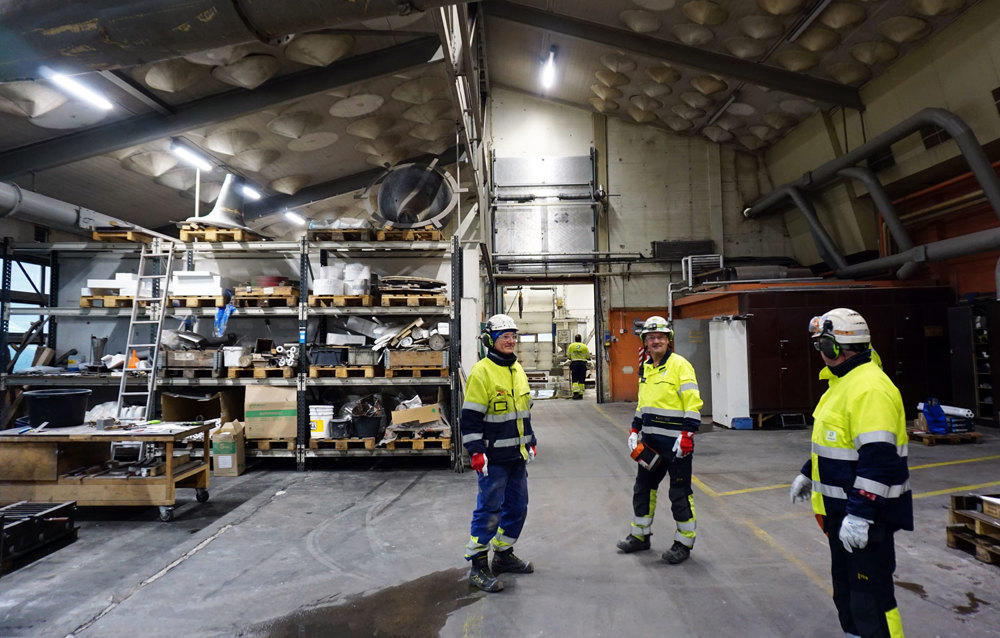
Driving innovation together
Product development is a vital aspect of Bilfinger Refractory’s contracts.
“We dedicate significant effort to developing new possibilities, methods, and materials in collaboration with customers and suppliers, enabling these advancements,” Herum explains. “We are committed to delivering continuous improvements for our clients.”
Bilfinger Refractory’s headquarters are located at Herøya, with 25 professionals attached to the department.