The project will improve the production capacity of PVC paste resin from 40 to 55 thousand tonnes a year. INOVYN answered for the process design, while Bilfinger was responsible for project management, detailed engineering, procurement and facility management.
What does the expansion mean for the PVC factory in Herøya?
"We are a small PVC factory seen from a European perspective," says Kari-Anne Leth-Olsen. She is the Production Manager of the PVC factory at Herøya and project owner of the 'Venus Project'. "The expansion makes us more robust, and PVC paste resin is the type of PVC on which we have the highest margins. We will not increase our manning levels, but will produce greater volumes with the same number of employees. This means that we will be a more sustainable organisation in the long-term, and that a successful project can now be the foundation for new growth – both for PVC paste resin and on PVC suspension resin."
PVC paste resin is used in soft products such as wallpaper, floor coverings, blood bags and anything else considered soft PVC. S-PVC is used in pipes, window profiles and other hard products. S-PVC is a more common product.
"INOVYN is Europe's largest PVC manufacturer and we have strengthened our position in the organisation. We are extremely pleased that INOVYN has chosen to invest here at Herøya Industrial Park. It was not a matter of course. We are competing for investment funds with all the other factories in the group, which means management is confident that we can do things well here in Porsgrunn. The investment means that workplaces here in Porsgrunn are even safer going forward."
Upgrades and new equipment
"The majority of the factory is still the same. We have introduced changes and modifications to existing process equipment to increase the capacity. And then we have built a completely new dryer and a powder conveyor system in a new building."
The new building is the single largest element in the project, with an area of approx. 250 square metres and a height of approx. 30 metres including the flue.
After the handover INOVYN is in full swing testing equipment and some installations have been put into production. "We expect to spend the period up until the first week of July on testing. We are doing this work ourselves."
"We have chosen to take responsibility for the process design ourselves," adds Leth-Olsen. "We have taken responsibility that this plant will maintain the production capacity we have calculated, but we have not yet verified it. Hopefully, we will do this in July/August. So far the tests are promising."
Expansion during full production
"The work has been partly done during full production at the factory. We began excavating in March 2019," says Jonny Olsen. He is employed by Bilfinger and has been brought in at INOVYN as project manager of the team responsible for detailed engineering, procurement and facility management on behalf of INOVYN.
The project team consists of employees from Bilfinger, Sweco, TS Group and INOVYN. Employees from the different companies have been closely integrated throughout the entire process, and the organisation has worked well throughout the entire period.
"PVC and everyone who works there are a pleasure to collaborate with. INOVYN knows what it wants and it demands the best. Which is a strength in itself. It's quite easy to run a project when you have a meticulous developer. Everyone in the team has been committed and delivered quality," emphasizes Olsen.
Perhaps 'Venus 2' will arrive
"The entire organisation is looking forward to the challenge of starting up a partly new factory," says Leth-Olsen. "We now have a new facility and have the opportunity to optimize production. The vast majority in our organisation believe we should certainly manage 55 thousand tonnes a year. We will not stop until we know that we have reached maximum capacity."
"We have already introduced Venus 2. This means an increase in capacity to 90 thousand tons of ´PVC paste resin annually. We will then start using the old dryer, which will be put 'out to graze' after this project. If we are to get investment funds for the next project, we need to succeed now and show that it is right for INOVYN to invest in Grenland," says the production manager.
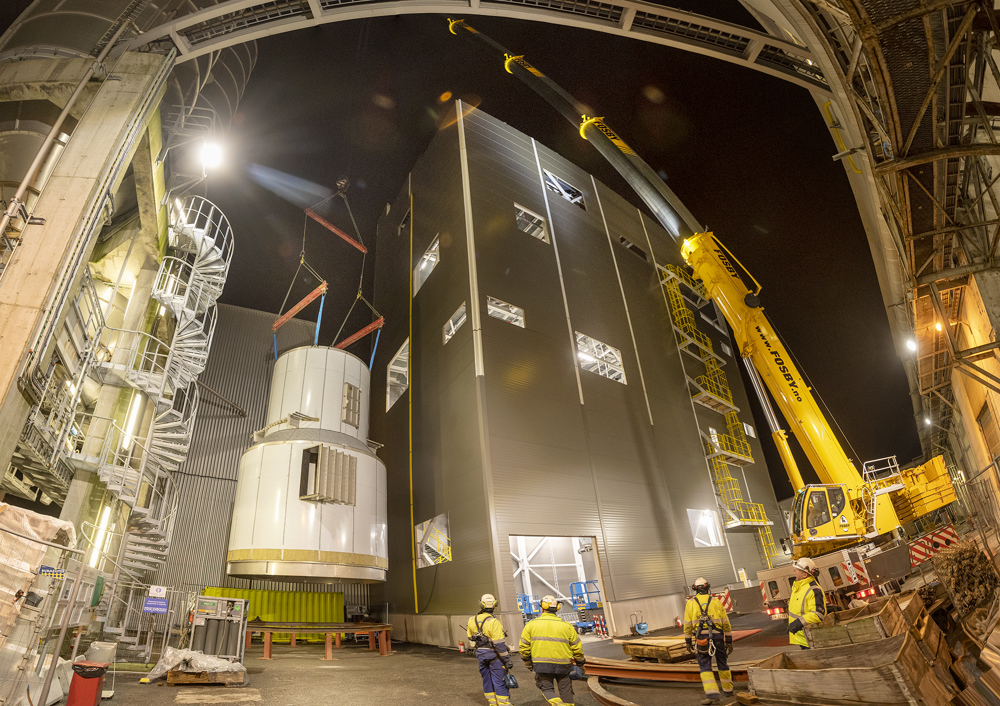
Close to stopping
"The corona crisis reached us towards the end of the the project," adds Leth-Olsen. "We nearly stopped the entire project to shield operations and not risk downtime in production."
"We were delayed some five weeks, says Olsen. "It becomes very complex when something like this happens. We had a great deal of foreign workers. Some we had to send home immediately after the shutdown, while others we didn't dare take back after the Easter holiday. Luckily, the contractors managed to get people who were actually planned to be stationed else where in Norway. It was demanding to replace the workforce during the run-in. The new employees needed to get up to speed with the work, they had to complete security clearance and become familiar with the workplace. This takes time. However, even though there was a delay to the original plans, we were able to reach our target.
14. July 2020