Lehrmann refers to the industrial environment as dynamic, and believes it will be possible to obtain the right skills for the company going forward. The company has appointed its first few operators and makes regular deliveries to customers – even though production is still at its pilot stage.
Jens Lehrmann, electrochemical engineer, has worked at various industrial companies and joins Seram Coatings from his position at Saint Gobain, where he was employed as a unit working with silicon carbide. “That was how I got into this business.”
Silicon carbide is an industrial mineral that does not occur naturally, it has to be processed at smelting plants. The oldest plant in the world was founded by Sam Eyde in 1912 and is situated in Arendal. “The company in Arendal gradually became part of Saint Gobain. I joined the company as a salesman and gradually took over professional responsibility for a number of technical ceramics as a product line manager.”
Sales at a high technical level
“When Seram Coatings was looking for a new general manager focusing on technical sales and industrialisation, the job was absolutely perfect for me. I have experience of complex professional sales processes”.
"Replacing tungsten carbide with our product will result in a weight reduction of around 80 per cent.
Jens Lehrmann
Silicon carbide can be used as an abrasive, and it can be used as a raw material in the industry. As the name indicates, Seram Coatings uses the raw material in various coatings. The company creates the powder that is sprayed onto various wear parts to make them more resistant to wear.
From pilot to industrial production
In parallel with his sales job, Lehrmann is now busy helping the product to make the transition from the pilot phase to industrial production. “We have a pilot line, and we know how we should upscale to the first industrial stage, but we have to make sure this upscaling is in line with what our customers need.”
What point have you reached in the process?
“We’re holding discussions with our customers,” explains Lehrmann, “and we’re sending out test materials to help us determine what they need so that we make the right choices. I feel we’re quite close to taking the next step. We’re developing the pilot in line with our customers’ requests, and we’re expanding our capacity according to needs and demands.”
Does this mean that Seram Coatings isn’t waiting for a technological breakthrough, but a breakthrough in the market before you can invest in production capacity?
“We haven’t quite reached our target when it comes to technology, but the most important thing at the moment is to put marketing-related aspects into place. We still have to work on engineering and R&D in respect of our products, but I reckon most of our challenges are with marketing rather than the technology. We have faith in our technology.”
Customers in the aviation, automotive and technical industries
Who are your customers?
“I’d rather not say too much about that, but in the long run we reckon engines for vehicles and aircraft are extremely interesting. Our technology is fairly unique, and we want the tungsten carbide currently used to be replaced with our product. That will result in a weight reduction of around 80 per cent. This means an aircraft engine could save quite a bit of weight, and that’s very important. Rotary equipment is another area we’re looking at. Balancing rotation becomes less critical when you can reduce the weight of the thing that rotates. So I reckon our major segments are the aviation and automotive industries and technical industry.”
Is Seram Coatings about to make some major investments in the industrialisation process?
“Of course we’re about to invest millions, and we have to work out how we’re going to finance that expansion. We’re making powder for coatings at present, but on a pilot scale, not an industrial scale.
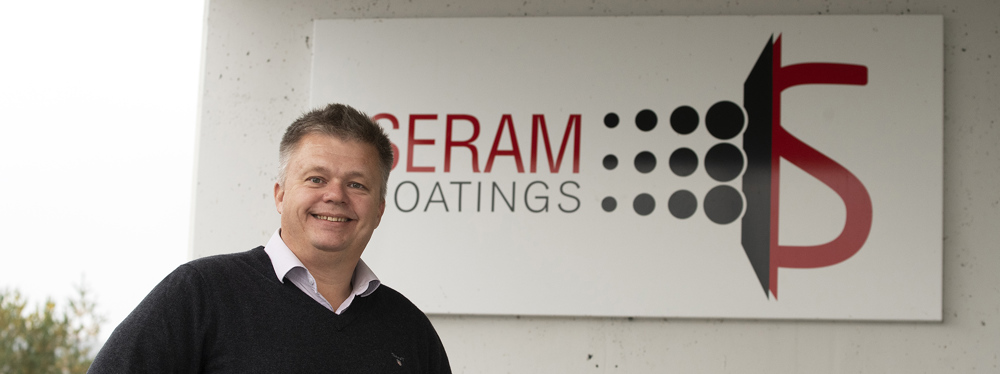
Focusing on 2020
Seram Coatings now has around 10 employees divided between production at Herøya and technological development at the Norwegian University of Science and Technology in Trondheim. “We’ve taken on a number of talented process operators,” explains Lehrmann. “And that’s exactly what we need now that we’re about to grow. We are not looking for more staff right at the moment, but we’ll be needing more hands on deck when we upscale.”
How big could the company become?
The former principal of the Norwegian University of Science and Technology told TA that the company has the potential to turn over billions. I don’t really want to comment on that statement. Now we’re going to focus on acquiring the customers we need and implementing the first stage by industrialising pilot production. This will turn Seram Coatings into a good, healthy company,” he says. “I’m focusing on what we’re going to be doing in 2020. We won’t be turning over billions just yet, in any case. But even so, working with this is extremely enjoyable, and we think we’re going to be able to establish a long-term industrial company that will remain at Herøya for a long time to come,” he concludes.
17. October 2019